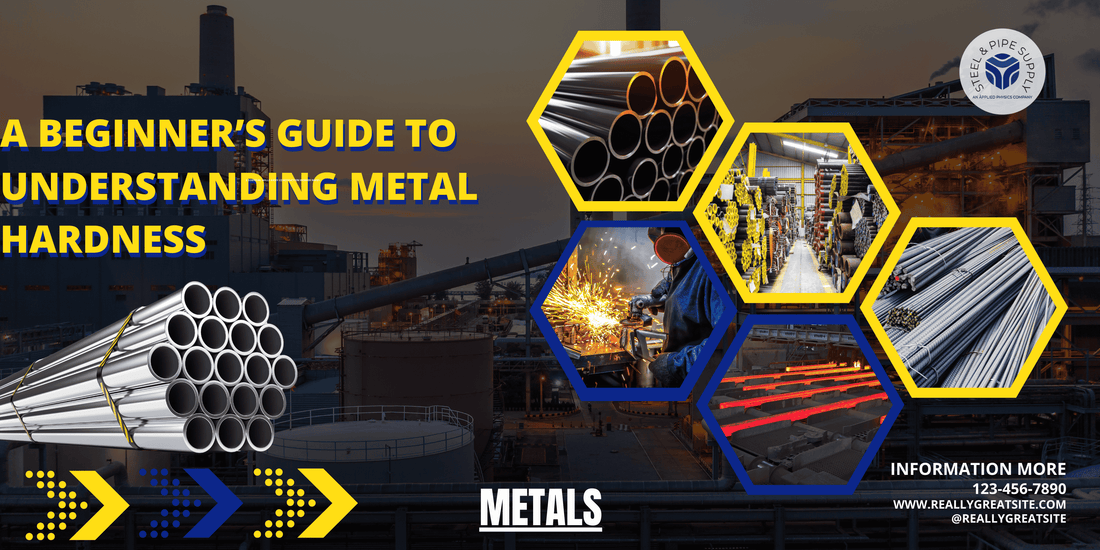
A Beginner’s Guide to Understanding Metal Hardness
Share
Introduction
Metal hardness refers to the ability of a metal to resist deformation, indentation, or scratching. It is a crucial mechanical property that determines the metal's suitability for specific applications. Hardness is not to be confused with strength, which is the ability of a material to withstand an applied force without failure.
Instead, hardness is a measure of a metal's resistance to localized plastic deformation. In simpler terms, the metal can maintain its shape under stress or load. Understanding metal hardness is essential for engineers, metallurgists, and manufacturers as it directly impacts the performance and durability of metal components in various industries.
Metal hardness can be influenced by several factors, including the metal's composition, microstructure, heat treatment, and manufacturing processes. These factors collectively determine the metal's ability to withstand wear, abrasion, and impact, making hardness a critical consideration in material selection for different applications.
Key Takeaways
- Metal hardness refers to the ability of a metal to resist deformation, indentation, or scratching.
- Factors affecting metal hardness include the type of metal, its composition, heat treatment, and manufacturing processes.
- Common methods for measuring metal hardness include Brinell, Rockwell, and Vickers hardness tests.
- The Rockwell hardness scale is widely used and measures the indentation hardness of a material.
- Metal hardness is important in various applications such as manufacturing, construction, and engineering, and can be improved through heat treatment and alloying.
Factors Affecting Metal Hardness
Alloying Elements and Microstructure
Alloying elements such as carbon, chromium, nickel, and manganese can significantly impact the hardness of a metal. For instance, carbon steel with higher carbon content tends to be harder than low-carbon steel due to the formation of carbides within the microstructure.
Heat Treatment and Manufacturing Processes
Additionally, the heat treatment process, including quenching and tempering, can alter the microstructure of the metal, thereby affecting its hardness. Furthermore, the manufacturing process can also influence metal hardness. For instance, cold working or strain hardening can increase the hardness of certain metals by introducing dislocations and defects in the crystal structure.
Optimizing Hardness for Specific Applications
On the other hand, annealing processes can reduce hardness by relieving internal stresses and promoting grain growth. Understanding these factors is crucial for controlling and optimizing the hardness of metals for specific applications.
Common Methods for Measuring Metal Hardness
There are several methods for measuring metal hardness, each with its unique principles and applications. Some common methods include Brinell, Rockwell, Vickers, and Knoop hardness tests. The Brinell test involves indenting a hardened steel or carbide ball into the surface of the metal and measuring the diameter of the impression to determine the hardness value.
The Rockwell test utilizes different combinations of applied loads and indenters to measure the depth of penetration into the metal surface. The Vickers and Knoop tests are based on similar principles but use pyramidal diamond indenters to measure hardness. These methods provide valuable insights into the material's resistance to plastic deformation and are widely used in quality control and material characterization processes across various industries.
Understanding the Rockwell Hardness Scale
Rockwell Hardness Scale | Description |
---|---|
A | Used for soft metals |
B | Used for harder metals and alloys |
C | Used for thin materials and surface treatments |
D | Used for hardened steels and cemented carbides |
E | Used for thin steel and shallow case-hardened steel |
The Rockwell hardness scale is one of the most commonly used methods for measuring metal hardness due to its simplicity and versatility. It utilizes different scales designated by letters such as A, B, C, D, E, F, and K, each tailored for specific materials and testing conditions. For instance, the Rockwell C scale is commonly used for measuring the hardness of hardened steels and other hard materials, while the Rockwell B scale is suitable for softer metals and alloys.
The Rockwell hardness test involves applying a minor load to set the position of the indenter on the surface of the metal, followed by applying a major load to penetrate the surface. The depth of penetration is then measured and converted into a numerical value on the Rockwell scale. Understanding the Rockwell hardness scale is essential for accurately assessing and comparing the hardness of different metals and alloys.
Importance of Metal Hardness in Different Applications
Metal hardness plays a critical role in various industrial applications, including manufacturing, construction, automotive, aerospace, and tooling. In manufacturing processes, harder metals are often preferred for tooling and dies to withstand wear and deformation during shaping and forming operations. In construction, materials with high hardness are used for structural components and wear-resistant surfaces to enhance durability and longevity.
In the automotive and aerospace industries, metal components with specific hardness levels are crucial for ensuring safety, reliability, and performance under extreme conditions. Furthermore, in tooling and machining applications, selecting metals with appropriate hardness is essential for achieving precision, surface finish quality, and tool longevity. Understanding the importance of metal hardness in different applications is vital for optimizing material selection and design considerations.
How to Improve Metal Hardness
There are several methods to improve the hardness of metals based on their composition and microstructure. Alloying elements such as carbon, chromium, and vanadium can be added to enhance the hardness of steel alloys through solid solution strengthening or precipitation hardening mechanisms. Heat treatment processes such as quenching and tempering can also be employed to achieve specific hardness levels by controlling the microstructural transformations within the metal.
Furthermore, surface treatments such as carburizing, nitriding, and ion implantation can be utilized to create hardened surface layers on metals while maintaining a tough core. These methods are commonly employed to improve wear resistance and extend the service life of components in demanding applications. Understanding these techniques is essential for tailoring the mechanical properties of metals to meet specific performance requirements.
Tips for Selecting the Right Metal Hardness for Your Project
When selecting a metal for a particular project or application, it is essential to consider various factors such as load conditions, wear mechanisms, operating temperatures, and environmental exposure. For high-wear applications, materials with high hardness and wear resistance such as tool steels or cemented carbides may be preferred. In contrast, for applications involving impact or shock loading, toughness may be prioritized over extreme hardness.
Additionally, considering factors such as machinability, weldability, corrosion resistance, and cost-effectiveness is crucial in selecting the right metal hardness for a project. Collaborating with materials engineers or metallurgists can provide valuable insights into material selection based on specific performance requirements and constraints.
Conclusion
Understanding metal hardness is essential for engineers, designers, and manufacturers across various industries. By considering factors affecting metal hardness, common measurement methods such as Rockwell scale, importance in different applications, methods for improvement, and selection tips, individuals can make informed decisions regarding material selection and design considerations to optimize performance and durability in their projects.