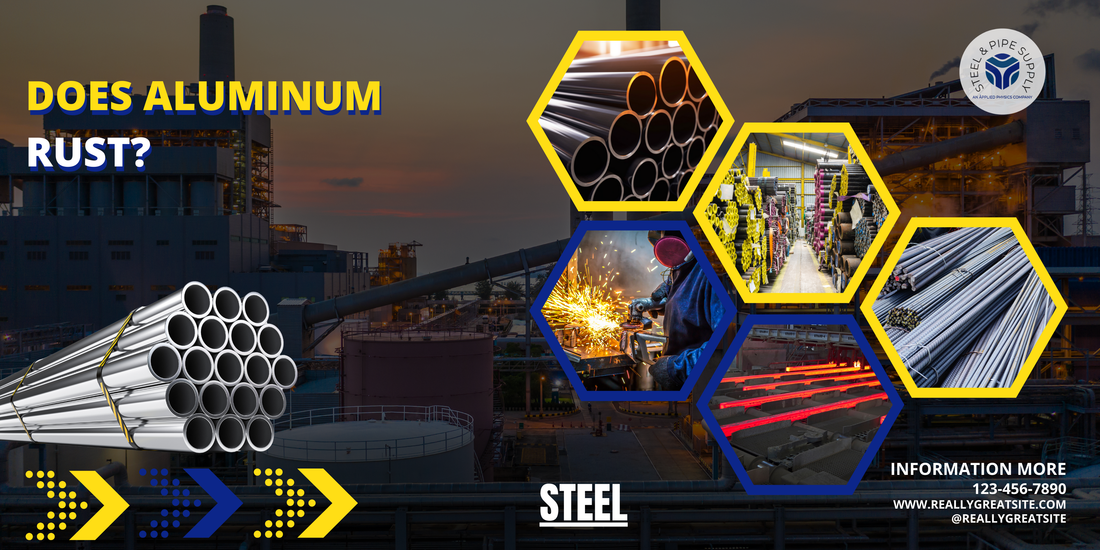
Does Aluminum Rust?
Share
Aluminum is a lightweight, silvery-white metal that constitutes the third most abundant element in the Earth's crust, comprising approximately 8% of the planet's soil and rocks. Its exceptional versatility enables its widespread use across various industries, including construction
, transportation, packaging, and electrical wiring. One of aluminum's key characteristics is its remarkable resistance to corrosion, making it an ideal material for outdoor and marine applications where exposure to harsh environments is inevitable.
Additionally, aluminum is non-toxic, non-magnetic, and non-sparking, rendering it suitable for use in sensitive environments such as food processing and medical equipment. Aluminum boasts a high strength-to-weight ratio, making it an attractive material for structural applications where weight reduction is crucial. Its high malleability and ductility enable it to be easily formed into complex shapes and structures, further expanding its range of applications.
Furthermore, aluminum exhibits excellent thermal and electrical conductivity, solidifying its popularity in the manufacture of heat exchangers, electrical transmission lines, and other applications where these properties are paramount. Overall, aluminum's unique combination of properties makes it a highly versatile material with a broad range of applications across various industries.
Key Takeaways
- Aluminum does not rust, but it can corrode under certain conditions.
- Aluminum is a lightweight, non-magnetic, and non-toxic metal with high resistance to corrosion.
- The corrosion process in aluminum is mainly caused by oxidation and can be accelerated by factors such as exposure to moisture, salt, and acidic environments.
- Preventing aluminum corrosion involves using protective coatings, anodizing, alloying, and proper maintenance.
- Aluminum corrosion is different from rust, as rust specifically refers to the corrosion of iron and its alloys.
Understanding the Corrosion Process in Aluminum
The Formation of Aluminum Oxide
In the case of aluminum, the most common form of corrosion is known as aluminum oxide, which forms a thin, protective layer on the surface of the metal. This layer acts as a barrier, preventing further corrosion from occurring.
Risks of Corrosion
However, if the protective oxide layer is damaged or compromised, aluminum can begin to corrode. This can happen as a result of exposure to harsh chemicals, high temperatures, or mechanical damage. Additionally, aluminum can also undergo galvanic corrosion when it comes into contact with other metals in the presence of an electrolyte, such as saltwater.
Importance of Understanding Corrosion
Understanding the corrosion process in aluminum is important for identifying potential sources of corrosion and implementing effective prevention measures. By recognizing the risks and taking steps to prevent corrosion, the durability and lifespan of aluminum can be significantly extended.
Factors that Contribute to Aluminum Corrosion
There are several factors that can contribute to aluminum corrosion. One of the most common causes is exposure to harsh environmental conditions, such as saltwater or acidic rain. These conditions can accelerate the corrosion process and lead to the breakdown of the protective oxide layer on the surface of the metal.
Additionally, exposure to high temperatures can cause aluminum to undergo rapid corrosion, particularly in the presence of moisture. Another factor that can contribute to aluminum corrosion is contact with dissimilar metals in the presence of an electrolyte. This can lead to galvanic corrosion, where one metal acts as an anode and the other as a cathode, leading to accelerated corrosion of the anode.
Mechanical damage, such as scratches or dents, can also compromise the protective oxide layer on aluminum and make it more susceptible to corrosion. Understanding these factors is important for implementing effective corrosion prevention measures.
How to Prevent Aluminum from Corroding
Question | Answer |
---|---|
Does Aluminum Rust? | No, aluminum does not rust. It forms a thin layer of oxide on its surface that protects it from corrosion. |
Corrosion Resistance | Aluminum has high corrosion resistance due to the oxide layer that forms on its surface. |
Applications | Aluminum is commonly used in outdoor structures, aerospace industry, and food packaging due to its corrosion resistance. |
There are several methods that can be used to prevent aluminum from corroding. One of the most effective ways to protect aluminum from corrosion is through the use of protective coatings. These coatings act as a barrier, preventing moisture and oxygen from coming into contact with the metal surface.
There are many different types of coatings available, including paints, anodizing, and powder coatings, each with its own set of advantages and limitations. Another effective method for preventing aluminum corrosion is through the use of alloying elements. By adding small amounts of other metals to aluminum, it is possible to improve its resistance to corrosion.
For example, adding magnesium or zinc to aluminum can help to enhance its protective oxide layer and make it more resistant to corrosion. Additionally, proper design and maintenance practices can help to minimize the risk of corrosion in aluminum structures and components.
Differences Between Aluminum Corrosion and Rust
While aluminum does not rust in the same way that iron does, it can still undergo a form of corrosion that is similar in some ways. The main difference between aluminum corrosion and rust is the appearance of the corrosion products. When iron rusts, it forms a reddish-brown flaky layer of iron oxide on the surface of the metal.
In contrast, when aluminum corrodes, it forms a white or grey powdery substance known as aluminum oxide. Another key difference between aluminum corrosion and rust is the way in which the corrosion products interact with the metal surface. In the case of iron rust, the corrosion products can continue to build up over time, leading to further degradation of the metal.
In contrast, the formation of aluminum oxide creates a protective barrier on the surface of the metal, preventing further corrosion from occurring.
Common Misconceptions about Aluminum Corrosion
Myth: Aluminum is Completely Corrosion-Proof
While it is true that aluminum has a natural resistance to corrosion due to its protective oxide layer, it is still susceptible to certain forms of corrosion under certain conditions.
Varying Levels of Corrosion Resistance
Another common misconception is that all forms of aluminum are equally resistant to corrosion. In reality, different alloys and grades of aluminum can have varying levels of resistance to corrosion, depending on their composition and processing history.
Managing Aluminum Corrosion
There is a misconception that once aluminum begins to corrode, there is no way to stop or reverse the process. In fact, there are many effective methods for preventing and managing aluminum corrosion.
Applications of Aluminum in Corrosion-Resistant Environments
Despite its susceptibility to corrosion under certain conditions, aluminum is still widely used in a variety of applications where resistance to corrosion is important. One common application for aluminum in corrosion-resistant environments is in marine structures and components. Aluminum's natural resistance to saltwater corrosion makes it an attractive choice for use in boats, docks, and other marine applications.
Another important application for aluminum in corrosion-resistant environments is in the construction industry. Aluminum is often used in building facades, roofing systems, and other architectural elements where resistance to environmental corrosion is important. Additionally, aluminum is commonly used in aerospace applications where its lightweight and corrosion-resistant properties are highly valued.
In conclusion, while aluminum does not rust in the same way that iron does, it is still susceptible to certain forms of corrosion under certain conditions. Understanding the factors that contribute to aluminum corrosion and implementing effective prevention measures are important for ensuring the long-term performance and durability of aluminum structures and components. By using protective coatings, alloying elements, proper design practices, and maintenance procedures, it is possible to minimize the risk of corrosion in aluminum and extend its service life in a wide range of applications.